Обычные установки. Наименование «высоковакуумные системы» относится к установкам, в которых можно получать разрежение газа до давлений ниже lp.Hg. Иногда условия эксперимента требуют очень низких давлений (10-3—10-5 pHg). Установки, позволяющие получать такие давления, следует, пожалуй, называть «сверхвысоковакуумными». В настоящей главе рассматриваются только высоковакуумные установки.
Обычные установки состоят из следующих элементов:
-
1. Пароструйный насос с большой быстротой откачки и достаточно высоким предельным вакуумом, способный работать при выпускном давлении 20—30pHg.
-
2. Вспомогательный пароструйный насос («бустерный насос»), имеющий меньшую быстроту откачки, но способный работать при выпускном давлении lOOpHg и выше. Этот насос позволяет пользоваться менее высоким предварительным разрежением, чем это требуется в случае одного высоковакуумного насоса.
-
3. Насос предварительного разрежения, который создает и поддерживает необходимое для вспомогательного насоса выпускное давление и работает против атмосферного давления. Обычно для этой цели пользуются механическим насосом. В некоторых случаях, когда нужно откачивать большие количества газа, оправдывает себя применение трех- и четырехступенных пароструйных эжекторных насосов.
-
4. Охлаждаемая ловушка, помогающая работе высоковакуумного насоса тем, что она вымораживает из системы воду и другие конденсируемые вещества. Охладителем в таких ловушках служит жидкий воздух или жидкий азот.
-
5. В случае большого количества водяных паров необходимо ставить охлаждаемые ловушки, предотвращающие попадание паров в насосы предварительного разрежения. Температура ловушек должна быть —70° С или ниже. В качестве охладителя часто применяется сухой лед (СО2).
-
6. Всякого рода краны, вентили и манометры, необходимые для управления установкой Так как обойтись без этих элементов нельзя, следует предусматривать их с самого начала конструирования.
Фиг. 17 изображает обычную схему установки. На диаграмме показано приблизительное распределение давления в системе. Истинное распределение зависит, однако, от конкретного вида конструктивных элементов установки и режима их работы. Если бы понадобилось получить сверхвысокий вакуум, то схему при шлось бы изменить, поместив в высоковакуумную часть установки
какие-нибудь газопоглотители. Кроме того, возможно, потребовалось бы откачивать всю высоковакуумную часть через ловушку, вымораживающую пары самого пароструйного насоса. Давления более низкие, чем давление паров масла или другой рабочей 5* жидкости насоса, могут быть получены только таким способом. Это условие не относится к эжекторным насосам с большой скоростью струи, которые работают при достаточно большом давлении и в которых вязкостный поток ещо не переходит в молекулярный.
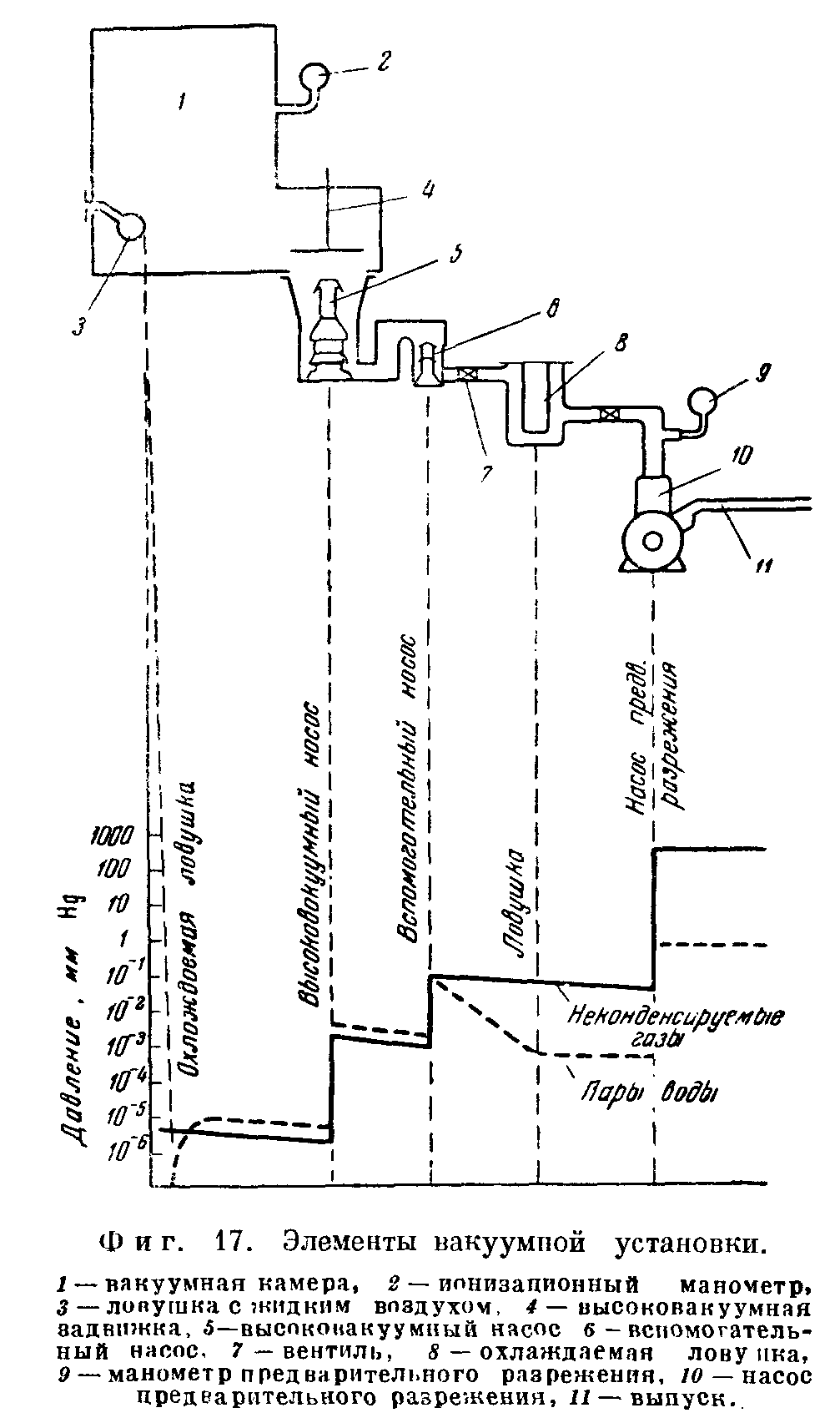
Механические насосы. Большинство современных насосов предварительного разрежения — механические насосы разной конструкции, с весьма различной быстротой откачки. Последняя определяется объемом, вытесняемым подвижной частью насоса за единицу времени, п, следовательно, зависит от числа оборотов мотора насоса. Производятся насосы с быстротой откачки от нескольких десятых до 300 л/сек. Самые маленькие насосы ставятся на течеискателп, масс-спектрографы, установки для распыления металлов и т. д., а самые большие обслуживают различные производственные объекты.
Все модели насосов построены на одном принципе, хотя конструктивно и различаются между собой. Основные типы насосов несколько отличаются друг от друга по характеристикам и условиям ухода за ними.
Уплотнителем во всех насосах служит масло. Все узкие зазоры механического насоса находятся в масле, препятствующем обратному протоку или натеканию газов.
Предельный вакуум насоса, т. е. самый высокий вакуум, который может дать насос, определяется следующими факторами:
-
1. Давление паров масла и примесей.
-
2. Растворимость откачиваемого газа в масле.
-
3. Величина вредного пространства, из которого газ механически не выбрасывается при работе насоса.
-
4. Качество масляного уплотнения.
-
5. Герметичность корпуса и подшипников вала.
Основная рабочая часть всех насосов — эксцентрический ротор, разгораживающий объем насоса на несколько объемов. Это достигается либо соприкосновением вращающегося эксцентрика с* поверхностью статора («золотниковый насос» Кинней), либо применением подвижных лопастей. При этом последние могут находиться в скользящем контакте с эксцентриком, будучи закрепленными на статоре («пластинчато-статорный пасос» Сенко), или скользить по внутренней поверхности статора, вращаясь вместе с ротором («пластинчато-роторный насос» Бич-Рэс).
Во всех насосах в рабочий объем в момент его увеличения засасывается значительное количество масла, которое затем вытесняется вместе с захваченным газом, когда объем сжимается до минимума при выпуске. Благодаря этому количество газа, остающегося в объеме при сжатии, очень невелико, так как вред ное пространство, остающееся между статором и эксцентриком, заполняется маслом. Выпускной клапан предохраняет насос
от обратного проникновения газа из атмосферы (фиг. 18). В ма леньких насосах обычно ставится пружинный клапан, который представляет собой кусок тонкой стальной пружинящей ленты,
прижимающейся к шлифованной поверхности выпускного отверстия. В больших насосах применяются тарельчатые клапаны.
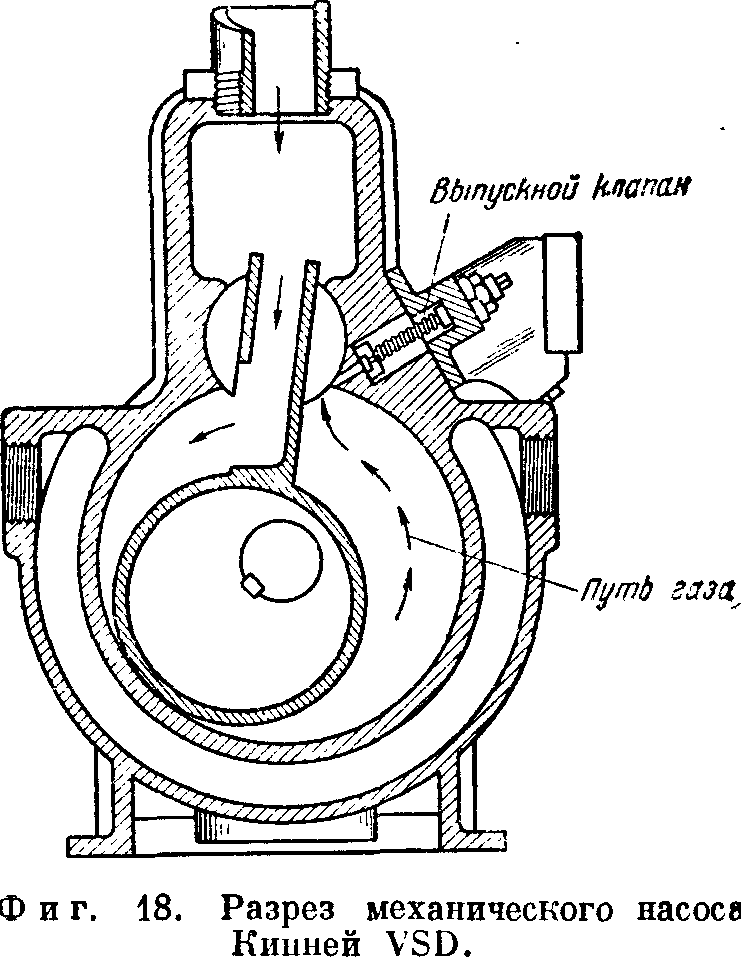
усмотреть защитные устройства от попадания в насос твердых
Зазоры между движущимися частями насоса должны быть малы, так как герметичность насоса обеспечивается масляной пленкой между рабочими поверхностями. Уплотнение больших зазоров этой пленкой затруднительно. Повреждение рабочих поверхностей выводит насос из строя, поэтому следует прединородных тел, как-то: гаек, болтов, кусочков металла, разбрасываемых при сварке. Для этой цели пригодна редкая сетка с соответствующей ловушкой. Частые сетки значительно снижают быстроту откачки, так что их не следует ставить на вакуумной стороне насоса.
Эксцентрик приводится в движение валом, ввод которого в насос должен быть герметичным, так как моторы, работающие в вакууме, пока еще не вошли в употребление. Существуют две системы уплотнения вращающихся валов. Первая система использует герметичное уплотнение между валом и корпусом. Вторая система более надежна, хотя, быть может, и не годится для насосов, к предельному вакууму которых предъявляются высокие требования. Ее принцип работы заключается в том, что к неплотностям между подшипниками и сальниками подается масло под атмосферным давлением. Таким образом, подшипники пропускают в систему не воздух, а масло. Правда, при этом туда попадает и воздух, растворенный в масле, но его количество практически незначительно.
Уже упоминалось, что быстрота откачки механических насосов определяется объемом, вытесненным за один оборот ротора. Если этот объем равен то быстрота откачки Sp= где / — число оборотов за единицу времени. Следовательно, если выражено в литрах, а / — число оборотов ротора за секунду, то Sp— быстрота откачки в литрах за секунду. Соответствующее количество газа определяется произведением S’ = jpVv гДе Р — плотность газа.
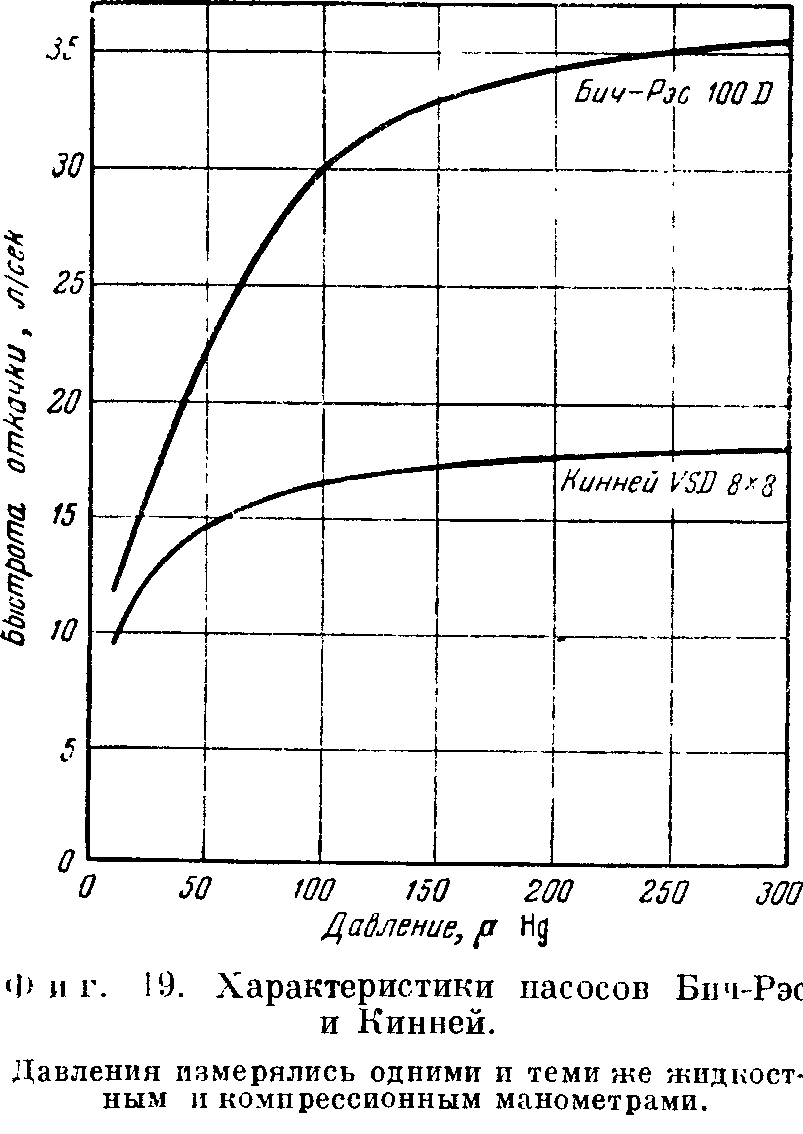
Нужно отметить, что производительность S' зависит от давления во впускном патрубке и, следовательно, не остается постоянной для насоса с данным числом оборотов.
Практически быстрота откачки также не остается постоянной. Дело в том, что с понижением давления все сильнее сказывается ограниченная проводимость диафрагм и трубопроводов на вакуумной стороне насоса. На фиг. 19 приводятся характеристики двух промышленных насосов. На фиг. 20 эти же результаты выражены в процентах объемной эффективности насосов, т. е. отношения эффективной быстроты откачки к ее расчетной величине fV,.
Как показывает опыт, быстрота откачки всякого насоса возрастает пропорционально увеличению числа оборотов, но порча и износ при этом происходят также гораздо быстрее. Обнаружено, что при завышении числа оборотов приблизительно в полтора раза по сравнению с фирменными данными начинается уменьшение объемной эффективности. Кроме того, роторы механических насосов не сбалансированы, и увеличение числа оборотов сопровождается увеличением вибраций.
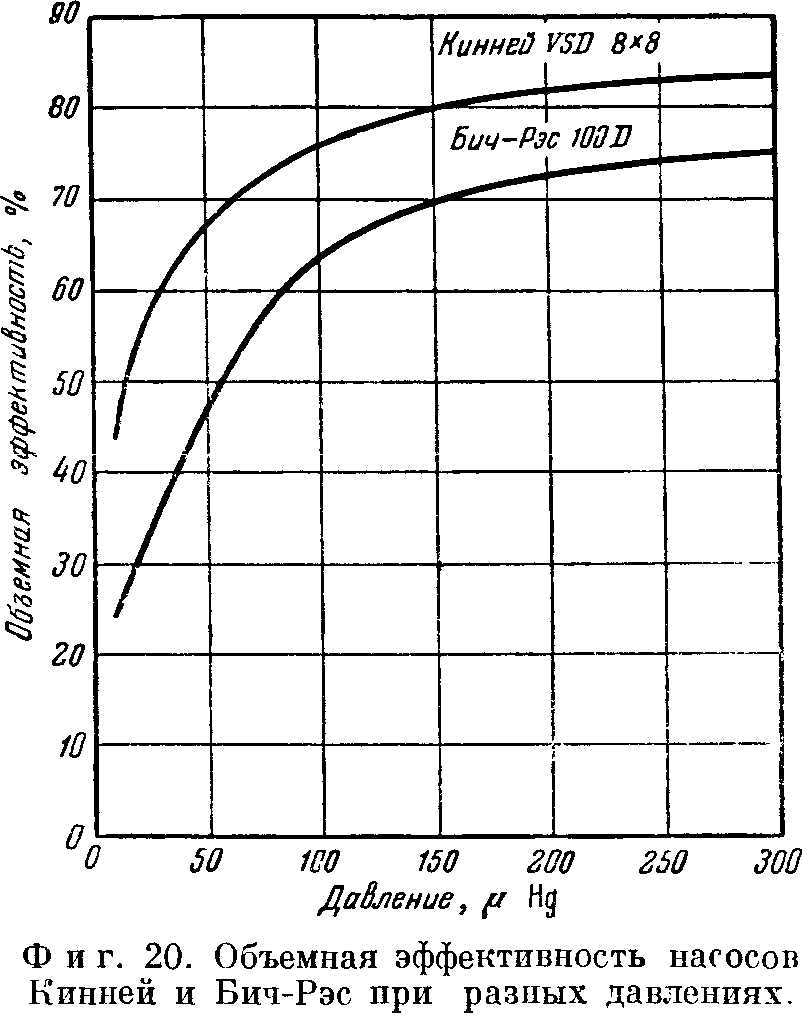
Все типы больших насосов и некоторые из малых имеют дополнительный масляный бачок, иногда являющийся конструктивным элементом установки. Во всех случаях масло, обычно под действием силы тяжести, подается к вакуумной камере через сальники подшипника и маслопроводы, причем приток масла регулируется специальными клапанами. Подача масла составляет от нескольких литров до десятков литров в час, в зависимости от размеров насоса и условий его работы. Масло, выбрасываемое в выпускной патрубок, попадает в специальный маслоуловитель, снова возвращается в бачок и т. д. Таким образом невозвратимый расход масла незначителен.
Приток масла к насосу определяется режимом работы. Если приток установлен при настройке на предельный вакуум, т. е. на самое низкое давление, которое может поддерживать насос в отсутствие потока газа, то при наличии потока газа этого масла уже нехватает для надлежащего уплотнения движущихся частей .
На нескольких насосах типа Кинней с производительностью 50 л[сек было сделано сравнение характеристик при изменении масляного питания насоса. Если не ставить себе задачей получение предельного вакуума, то разница невелика. На практике обычно стремятся получить не предельный вакуум, а максимальную быстроту откачки при более высоких давлениях, именно в области срыва работы вспомогательного пароструйного насоса. Следует заметить, что при впускном давлении 100 p.Hg большинство этих насосов в случае настройки на предельный вакуум дают вдвое меньшую быстроту откачки, чем при более обильной подаче масла.
Зависимость предельного вакуума от подачи масла в насос, вероятно, объясняется присутствием в масле растворенных газов. Чем меньше масла поступает в насос, тем меньше газов выделяется из масла при расширении объема.
У больших насосов (с быстротой откачки 20 л]сек и более) обычно предусматривается водяное охлаждение. К охлаждению предъявляются весьма умеренные требования: даже для самых больших насосов достаточно расхода воды в 5—10 л/мин. Маленькие насосы имеют воздушное охлаждение. Выделение тепла происходит в основном из-за механического трения, за исключением тех случаев, когда откачиваются большие количества газа, на пример при откачке установки от атмосферного давления. При этом насос может сильно нагреваться, однако на практике ему приходится работать в таких условиях весьма недолгое время.
Одной из основных причин плохой работы, а иногда и общей неисправности описанных насосов является загрязнение масла. При этом повышается давление масляных паров, что сильно портит предельный вакуум, а также происходит коррозия и осмаливание рабочих поверхностей насоса.
Повышение давления паров масла почти неизбежно в действующей установке. Обычно из системы откачивается достаточное количество паров воды, так что масло, циркулирующее в насосе, образует эмульсию с задерживающейся в нем водой. В случае обычно применяющихся масляных бачков с постоянным объемом этот процесс приводит к постепенному ухудшению вакуума. Тогда приходится спускать масло, промывать насос и заливать в него новое или регенерированное масло.
Если масло загрязняется только водой, то, для того чтобы осушить его перед возвратом в насос, достаточно постоянного протока теплого воздуха через масляный бачок. Это обычный способ удаления воды из очищенного масла, при котором маслу не причиняется никакого вреда. Существует множество промышленных маслорегенераторов, в которых горячее масло просасывается через сукновальную глину. При этом из масла удаляются все твердые примеси и летучие компоненты.
Если рабочее масло содержит разжижающие добавки и дру гие примеси, то следует позаботиться, чтобы эти вещества не удалялись при регенерации или чтобы они снова были введены в масло перед его подачей в насос. Известен случай, когда 14 насосов удовлетворительно работали на масле марки SAE-20. Однажды это масло было разбавлено турбинным маслом. Общая система непрерывной циркуляции масла имела регенератор с сукновальной глиной. После 4—5 часов работы все насосы остановились, так как масло в них загустело, причем рабочие поверхности оказались сухими и поцарапанными. После замены масла на первоначальное насосы попрежнему работали удовлетворительно.
Бороться с коррозией и осмаливанием поверхности труднее, чем с повышенной влажностью масла. В корпусах насосов, обычно литых, устанавливаются стальные валы, клапаны, пружины, бронзовые подшипники. Все эти металлические детали, а также и само масло, подвержены действию активных окисляющих агентов, как-то: SO2, Cl2, F2, а также кислот, ангидридами или производными которых являются эти окислители. Повидимому, коррозия металлических частей вследствие соприкосновения с окисляющими агентами, вообще говоря, невелика, за исключением стальных клапанов. Неоднократно отмечались неисправности пружинных клапанов вследствие разъедания их поверхностей. В некоторых случаях обнаруживается также разъедание чугунного гнезда, зашедшее настолько далеко, что приходится притирать клапаны заново.
Более часто насос выходит из строя из-за разрушения масел при окислении и из-за осаждения смолистых слоев на поверхностях насоса. В конце концов оседающая на роторе насоса смола прочно заклеивает насос. Приходится разбирать его и тщательно чистить каждую деталь. Подходящих для этой цели растворителей не имеется, так что обычно зачищают поверхности шабром из мягкого металла.
Насосы, в которых происходит осмаливание, иногда можно опознать по перегреву или скольжению ремня и, конечно, по ненормальному потреблению мощности. Если такой насос остановить, он заклеивается настолько, что его обычно не удается пустить снова. В этом случае необходимы разборка и чистка.
Как полагают некоторые операторы, им удавалось предотвратить осмаливание в остановленном насосе тем, что они перекрывали на время выключения водяное охлаждение и оставляли насос теплым, Пока нет надежных доказательств за или против этого убеждения. Однако, повидимому, справедливо, что если осмаливающийся насос не выключается и масло сменяется несколько раз в день, то на его поверхностях имеет место самоочистка. Имеются также указания, что насосы, уже бывшие в употреблении, менее подвержены осмаливанию, чем новые. Вероятно, это объясняется увеличением зазоров за счет износа.
Нормальное потребление энергии составляет около 0,75 кет на каждые 10 л/сек. Обычно такое отношение потребляемой мощности к быстроте откачки вполне удовлетворительно. В режиме, близком к заклеиванию, 4-киловаттный мотор на насосе с быстротой откачки 50 л/сек может перегореть.
Механические насосы испытывают, измеряя предельный вакуум, достигаемый насосом без нагрузки. Для такого измерения пригодны компрессионные манометры Мак Леода или теплоэлектрические манометры (например, манометр Пирани). Предельный вакуум несколько изменяется от образца к образцу и от марки к марке. Промышленные насосы, работающие на легких погонах автомобильного масла, например масле SAE-20, обычно имеют предельный вакуум от 5 до 20 p.Hg. Резкое ухудшение предельного вакуума по сравнению с приведенными данными может быть связано со следующими причинами:
-
1. Вода в масле. Если ухудшение вакуума объясняется этой причиной, то показателен внешний вид масла: сильно увлажненное масло мутно.
-
2. Регулировка клапанов масляного питания на слишком малую подачу масла. Если насос удовлетворительно работал ранее с такой же установкой клапанов, то, повидимому, ухудшение предельного вакуума произошло не поэтому.
-
3. Неисправность клапанов насоса из-за коррозии или из-за накопления грязи под ними. Последнее часто имеет место в практике. В этом случае поток воздуха, проникающий в насос в небольшой промежуток времени, резко ухудшает предельный вакуум. При коррозии ухудшение вакуума в большинстве случаев происходит постепенно.
-
4. Насос или манометр не герметичны. Насосы текут из-за плохой сборки. В процессе работы течь возникает редко.
Быстрота откачки механического насоса, измеренная при каком-нибудь заданном давлении, остается обычно постоянной. Производя повторные измерения быстроты откачки, можно обнаружить неисправности, которые иначе остались бы незамеченными. Для этого к системе присоединяют калиброванную течь и измеряют результирующее увеличение давления.
Быстрота откачки вычисляется по формуле

где ДР — изменение давления в микронах, а Е'атм.— величина течи в кубических сантиметрах за секунду при атмосферном давлении, Sp выражается в литрах в секунду.
Регулировать подачу масла следует из расчета максимальной быстроты откачки при заданном максимально допустимом давлении на впуске.
В некоторых случаях при измерении быстроты откачки обнаруживались дефекты сборки. Например, большие насосы Кинней в целях балансировки рабочих частей собирают из двух насосов, роторы которых сдвинуты на 180°. Если один из блоков поставлен клапанами наоборот, т. е. так, что засос происходит со стороны выпуска, то эта половина не принимает участия в откачке. Общая быстрота откачки насоса, собранного таким образом, вдвое меньше номинальной. Эту же неисправность можно, разумеется, заметить, измеряя время откачки сосуда с известным объемом от одного давления до другого.
Хорошо установленный механический насос современного промышленного образца почти не требует наблюдения. К монтажу насоса предъявляются следующие требования:
-
1. Насос должен быть неподвижно закреплен на бетонном основании.
-
2. Потребление мощности не должно превышать 0,75 кет на 10 л/сек. Следует применять соответствующие максимальные реле, защищающие мотор от перегрузки.
-
3. Не следует пользоваться дистанционными пускателями: можно не заметить, что насос заклеился, и пережечь мотор.
-
4. Нужно предусмотреть доступ к насосам для ухода за ними, например для смены масла.
В ряде случаев оправдывают себя некоторые усовершенствования, как-то: автоматическая или непрерывная подача масла и регенераторные установки. Очень хорошие результаты дает включение охлаждаемой ловушки для вымораживания воды перед насосом. Эти вопросы еще будут обсуждаться в настоящей главе.
Свойства масел, применяющихся в механических насосах, подробно не изучались. Вообще говоря, можно пользоваться турбинными маслами среднего веса. Желательными являются следующие свойства:
-
1. Судя по величине зазоров, в обычных насосах требуются масла SAE с номерами 15—20. Интервал рабочих температур в эксплоатационных условиях не очень широк, поэтому температурный коэффициент вязкости безразличен.
-
2. Наличие хорошего смазывания весьма существенно. Некоторыми маслами, очень стабильными к окислению, все-таки нельзя пользоваться без разжижающих добавок.
-
3. Способность масла образовывать эмульсии с водой должна быть как можно меньшей. Большинство маслоциркуляционных систем, которыми снабжены насосы, содержат отстойники для отделения воды от масла. Для получения вакуума, близкого к предельному для данного насоса, эти отстойники иногда оказываются недостаточными.
-
4. Масло должно быть устойчиво к окислению газами, подлежащими откачке. Можно пользоваться хлорированными или фторированными маслами, но они слишком дороги. Известны случаи успешного применения трикрезилфосфата. Это вещество иногда добавляется к автомобильным маслам для повышения их стойкости. В большинстве случаев удовлетворительно ведут себя дизельные и турбинные масла.
-
5. Масло не должно иметь летучих компонент с давлением пара, превышающим заданный предельный вакуум.
Скорость разрушения масел определяется условиями работы насоса. Насосы, откачивающие вакуумные системы, через которые протекает только воздух, непрерывно работают по нескольку месяцев без заметного ухудшения характеристик. Однако при откачке очень влажных контейнеров иногда приходится менять масло через несколько часов из-за образования масляной эмульсии. Если насос откачивает хлор, масло приобретает темный цвет (коричневый, пурпурный, иссиня-черный) из-за взвешенных в нем продуктов окисления; это не сказывается на вакууме, но может повести к осмаливанию. Если насос работает в таких условиях, приходится менять масло очень часто. Наиболее употребительные масла перечислены в приложении IV.
Большие насосы иногда выходят из строя при неправильном включении. Например, если насос Кинней был остановлен под вакуумом, то рабочий объем постепенно заполняется маслом, подающимся при атмосферном давлении. Большинство установок снабжено контрольным клапаном, автоматически перекрывающим подачу масла при выключении насоса. Эти клапаны не очень надежны. За время, пока насос не работает, в него может набраться значительное количество масла, которое при пуске должно быть выброшено из рабочего объеме насоса через выпускные клапаны уже при первом обороте, что весьма затруднительно ввиду большой скорости вращения мотора. Поэтому перед тем как включить мотор насоса, засосавшего масло, нужно провернуть его шкпв раз или два от руки. Довольно часто от резкого гидравлического удара, наблюдаемого при внезапном включении насоса с наполненной маслом рабочей частью, срезаются шпонки или ломается литье.
Чтобы не допускать засасывания масла в насос, а, возможно, и во всю установку, после выключения насоса в него следует напускать воздух. Даже у маленьких насосов с внутренним масляным резервуаром иногда происходит засасывание масла в соединенные с ними части вакуумной установки, хотя фирменные данные утверждают обратное.